日期:2017-01-10 / 人气: / 来源:www.biglss.com / 热门标签: z6尊龙旗舰厅 z6尊龙旗舰厅 z6尊龙旗舰厅
精益生产模式进入到中国已经接近20年了,具不完全统计在国内的具有一定规模的企业为例,外资企业中至少80%、国营企业至少60%、民营企业至少40%的企业都全面或部分导入过精益生产,就算没有导入精益生产的企业,只要是在制造行业工作的人至少都听过精益生产或tps丰田生产模式,也能说出几个5s管理、tpm等工具来。
本人从97年开始接触精益,2006年开始进入到咨询行业,为上百家企业进行过深入的咨询或培训服务,但每次面临怎么才能用最简洁、清晰的方式展示给我们客户精益生产到底是什么的时候都要犹豫不决,究其原因最关键的是我对精益的理解一直在发生变化。我发现自己对精益的接触越多,应用场景越广泛,精益在我心目中地位和用途越神圣。
这点疑问不仅仅是我,从精益的经典书籍的出版时间以及他们观点的变化也可以看出一二,如1990年出版的《the machine that changed the world改变世界的机器》重点阐述的是精益生产模式的诞生由来以及在现场直接可以看得到的各种工具的应用,到了1996年出版的《lean thinking精益思想》一书从简单的经验总结升华到方法论,把用精益思想5原则(确定顾客价值、识别价值流、价值流动、需求拉动、尽善尽美)的方式把精益生产的工作进行了较为完整的套路,到2011年出版的《the toyota way丰田模式》书籍已经从简单的方法论提升到更高的层面,它重点参数了精益制造的14项原则,这原则分为理念、尊重与合作、流程管理、问题解决,再具体一点的话,
一、理念:
1.管理决策以长期理念为基础,及时牺牲短期的财务收益也在所不惜(长期思维)
二、流程管理:
2.实现连续作业流程,使问题浮现(连续流)
3.利用拉动方式,避免生产过剩(拉动生产)
4.平抑工作量(均衡化)
5.出现质量问题时,立即停止生产(自働化)
6.为实现改善与授权,将任务标准化(标准化)
7.通过可视化管理,使问题无所隐蔽(可视化)
8.只采用可靠的、经过充分验证的技术(新技术)
三、尊重与合作
9.培养深谙公司文化、理念的管理人员(内部培养)
10.尊重、培养并挑战你的员工和团队(以人为本)
11.尊重、挑战并帮助你的供应商(共同成长)
四、问题解决
12.利用“持续改善”,使组织成为学习型组织(持续改善)
13.亲临现场,彻底了解情况(3现主义)
14.制定决策时要稳健,穷尽所有的选择,并征得一致同意(慢决策,快行动)
从这十四项原则中不难发现,理念、尊重与合作作为重点工作凸显出来了。而这些工作内容恰恰都是我们很难一眼看得到的,也就是说大家都已经发现简单学习精益的工具是很难真正体会到精益生产的核心,必须寻找企业精益转型更深层的、决定性的因素,而这些就是每年大批的标杆学习人员陆续到日本丰田工厂现场学习也很难学习到的关键因素。
今天我在办公室,迎接2017年的同时,重新梳理了一次精益生产架构,如下图个,供大家参考学习,以后有机会的时候对下图内容进行详尽的说明。
本人从97年开始接触精益,2006年开始进入到咨询行业,为上百家企业进行过深入的咨询或培训服务,但每次面临怎么才能用最简洁、清晰的方式展示给我们客户精益生产到底是什么的时候都要犹豫不决,究其原因最关键的是我对精益的理解一直在发生变化。我发现自己对精益的接触越多,应用场景越广泛,精益在我心目中地位和用途越神圣。
这点疑问不仅仅是我,从精益的经典书籍的出版时间以及他们观点的变化也可以看出一二,如1990年出版的《the machine that changed the world改变世界的机器》重点阐述的是精益生产模式的诞生由来以及在现场直接可以看得到的各种工具的应用,到了1996年出版的《lean thinking精益思想》一书从简单的经验总结升华到方法论,把用精益思想5原则(确定顾客价值、识别价值流、价值流动、需求拉动、尽善尽美)的方式把精益生产的工作进行了较为完整的套路,到2011年出版的《the toyota way丰田模式》书籍已经从简单的方法论提升到更高的层面,它重点参数了精益制造的14项原则,这原则分为理念、尊重与合作、流程管理、问题解决,再具体一点的话,
一、理念:
1.管理决策以长期理念为基础,及时牺牲短期的财务收益也在所不惜(长期思维)
二、流程管理:
2.实现连续作业流程,使问题浮现(连续流)
3.利用拉动方式,避免生产过剩(拉动生产)
4.平抑工作量(均衡化)
5.出现质量问题时,立即停止生产(自働化)
6.为实现改善与授权,将任务标准化(标准化)
7.通过可视化管理,使问题无所隐蔽(可视化)
8.只采用可靠的、经过充分验证的技术(新技术)
三、尊重与合作
9.培养深谙公司文化、理念的管理人员(内部培养)
10.尊重、培养并挑战你的员工和团队(以人为本)
11.尊重、挑战并帮助你的供应商(共同成长)
四、问题解决
12.利用“持续改善”,使组织成为学习型组织(持续改善)
13.亲临现场,彻底了解情况(3现主义)
14.制定决策时要稳健,穷尽所有的选择,并征得一致同意(慢决策,快行动)
从这十四项原则中不难发现,理念、尊重与合作作为重点工作凸显出来了。而这些工作内容恰恰都是我们很难一眼看得到的,也就是说大家都已经发现简单学习精益的工具是很难真正体会到精益生产的核心,必须寻找企业精益转型更深层的、决定性的因素,而这些就是每年大批的标杆学习人员陆续到日本丰田工厂现场学习也很难学习到的关键因素。
今天我在办公室,迎接2017年的同时,重新梳理了一次精益生产架构,如下图个,供大家参考学习,以后有机会的时候对下图内容进行详尽的说明。
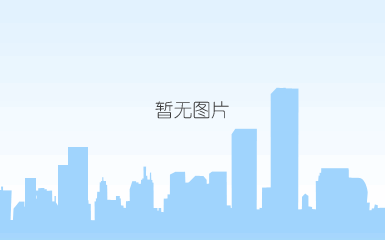
作者:博革咨询