日期:2017-07-06 / 人气: / 来源:www.biglss.com / 热门标签: z6尊龙旗舰厅
精益生产工具有哪些?上海博革企业管理咨询有限公司为您解读以下精益十大工具。
1.现场5s/6s管理与目视化
现场5s/6s管理与目视化工具的培训、学习,通过顾问的课堂练习及现场改善指导,学员可以快速掌握6s及可视化的管理的工具与方法,并掌握如何根据企业自身的实际情况,制定出切实可行的推进计划,打造一目了然的作业环境,建立职责清晰的作业秩序,保证高度自主的作业行为,提供安全有效的作业品质,用傻瓜式的生产说明和高度透明的日常管理来建立企业优秀的生产文化,促进车间现场生产信息的交流与互动,促进人、事、物管理上的视觉化、公开化、透明化、界限化、人性化,提高企业生产管理水平。
2.vsm价值流管理
vsm价值流管理运用相关精益原理分析企业当前价值流图,识别并消除本企业运作流程中存在的各种浪费,从而建立企业的未来精益价值流图,并设定相关精益价值流关键指标;根据规划的未来价值流图,制定精益改善计划并付诸实施,实现从传统生产模式转向精益生产模式的转化。
3.smed快速换模
smed快速换模法将可能的换线时间缩到最短(即时换线)。它可以将一种正在进行的生产工序快速切换到下一生产工序。快速换模法同时也常指快速切换。快速换模法能够并且常常是用于启动一个程序并快速使其运行,且处于最小浪费的状态。
4.防错改善
在生产制造过程中,无意识中会产生各种过程失误,制造过程不同,其失误的种类也会有区别,一般都会表现在人、机、料、法、环、测的不同层面上。为了解决或预防这些失误的产生所以要导入防错技术。防错的导入和使用,避免工作错误的发生,进而达到“第一次就把工作做对”,提升产品质量和作业效率。
5.标准作业
标准作业是:以人的动作为中心,以没有浪费的操作方法和顺序进行作业的方法。在目前看来,是最优的方法。标准作业的编制标准,就是必须满足“成败、安全、易做”。标准作业其实有两大目的:告诉员工“do right things”(政策)以及“do thing sright”(程序),知道哪些事能做或不能做,以及对的事情又该怎么才能做好。同时,告诉员工,在标准作业要点中,不按照标准作业进行操作,将可能导致的隐患,明确的告诉员工。所以,标准作业不能只有程序步骤,还必须阐明背后的道理,才能让员工在处理事务上,维持规范,也能保持合理的弹性。
6.看板拉动
拉动看板是一种用手工传递看板的方法,这些看板记录了补充物料需求的信息。其建立的目的是为使用小的、轻的、手工处理的包装箱来补充所需物料提供了一个基础系统。
7.ie-方法研究
对作业方法进行科学分析,从而对人,时间,材料等进行经济,合理,有效的设计使用,是一种对作业方法进行设计和改善的方法。研究对象包括原材料,工艺,作业流程,作业工具,设备布局及操作动作。
8.ie-时间分析
工作时间过程的直接测量,有时间分析及运转率分析等代表方法,测量上以直接测量和录像测量为主。或对作业单位细分化设定后,通过经验数据的合成设定时间的方法,如以标准数据以及统计数据库为依据进行标准时间的设定。
9.tpm管理
tpm(total productive maintenance–全员生产维护),从专业的角度上来说,是在管理方面是以提高企业的设备综合效率为目标,以生产全系统的预防维护为过程,以全员参与为基础的设备保养和维护的活动。
10.问题解决方法
为了创建有关解决问题的概念和工具的通用语言,为持续的改进提供系统方法。5w2h 、5why、pdca循环、异常管理、a3报告、qc7大工具等解决问题的方法实施。
1.现场5s/6s管理与目视化
现场5s/6s管理与目视化工具的培训、学习,通过顾问的课堂练习及现场改善指导,学员可以快速掌握6s及可视化的管理的工具与方法,并掌握如何根据企业自身的实际情况,制定出切实可行的推进计划,打造一目了然的作业环境,建立职责清晰的作业秩序,保证高度自主的作业行为,提供安全有效的作业品质,用傻瓜式的生产说明和高度透明的日常管理来建立企业优秀的生产文化,促进车间现场生产信息的交流与互动,促进人、事、物管理上的视觉化、公开化、透明化、界限化、人性化,提高企业生产管理水平。
2.vsm价值流管理
vsm价值流管理运用相关精益原理分析企业当前价值流图,识别并消除本企业运作流程中存在的各种浪费,从而建立企业的未来精益价值流图,并设定相关精益价值流关键指标;根据规划的未来价值流图,制定精益改善计划并付诸实施,实现从传统生产模式转向精益生产模式的转化。
3.smed快速换模
smed快速换模法将可能的换线时间缩到最短(即时换线)。它可以将一种正在进行的生产工序快速切换到下一生产工序。快速换模法同时也常指快速切换。快速换模法能够并且常常是用于启动一个程序并快速使其运行,且处于最小浪费的状态。
4.防错改善
在生产制造过程中,无意识中会产生各种过程失误,制造过程不同,其失误的种类也会有区别,一般都会表现在人、机、料、法、环、测的不同层面上。为了解决或预防这些失误的产生所以要导入防错技术。防错的导入和使用,避免工作错误的发生,进而达到“第一次就把工作做对”,提升产品质量和作业效率。
5.标准作业
标准作业是:以人的动作为中心,以没有浪费的操作方法和顺序进行作业的方法。在目前看来,是最优的方法。标准作业的编制标准,就是必须满足“成败、安全、易做”。标准作业其实有两大目的:告诉员工“do right things”(政策)以及“do thing sright”(程序),知道哪些事能做或不能做,以及对的事情又该怎么才能做好。同时,告诉员工,在标准作业要点中,不按照标准作业进行操作,将可能导致的隐患,明确的告诉员工。所以,标准作业不能只有程序步骤,还必须阐明背后的道理,才能让员工在处理事务上,维持规范,也能保持合理的弹性。
6.看板拉动
拉动看板是一种用手工传递看板的方法,这些看板记录了补充物料需求的信息。其建立的目的是为使用小的、轻的、手工处理的包装箱来补充所需物料提供了一个基础系统。
7.ie-方法研究
对作业方法进行科学分析,从而对人,时间,材料等进行经济,合理,有效的设计使用,是一种对作业方法进行设计和改善的方法。研究对象包括原材料,工艺,作业流程,作业工具,设备布局及操作动作。
8.ie-时间分析
工作时间过程的直接测量,有时间分析及运转率分析等代表方法,测量上以直接测量和录像测量为主。或对作业单位细分化设定后,通过经验数据的合成设定时间的方法,如以标准数据以及统计数据库为依据进行标准时间的设定。
9.tpm管理
tpm(total productive maintenance–全员生产维护),从专业的角度上来说,是在管理方面是以提高企业的设备综合效率为目标,以生产全系统的预防维护为过程,以全员参与为基础的设备保养和维护的活动。
10.问题解决方法
为了创建有关解决问题的概念和工具的通用语言,为持续的改进提供系统方法。5w2h 、5why、pdca循环、异常管理、a3报告、qc7大工具等解决问题的方法实施。
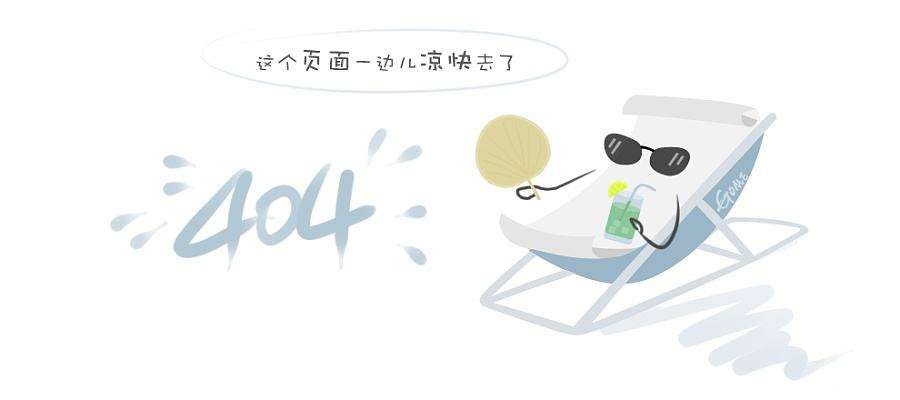
作者:博革咨询