日期:2017-02-10 / 人气: / 来源:www.biglss.com / 热门标签: 精益管理 精益生产 七大浪费
欢迎您访问博革咨询z6尊龙旗舰厅官网!博革咨询是中国首家整合精益生产/六西格玛/流程再造的咨询公司,专注于提供 精益生产、6s现场管理、tpm设备管理、精益工厂布局、专业目视化、精益供应链、精益研发、六西格玛管理、智能制造等综合性问题z6尊龙旗舰厅的解决方案并负责落地实施。
全国咨询热线:021-62373515、157-2153-3189
我们承诺:见效快、易复制,目标必对赌!
丰田生产方式是彻底消除浪费的方法,消除浪费就能提高生产率。制造现场的浪费是指「只会提高成本的要素」,存在’若不充分注意所有的地方浪费就会逐渐增加’的性质。因此制造产品的作业中, 需要有判断怎样的作业是浪费作业的能力。通过丰田生产方式的教育来培养发现‘浪费’的眼光。下面博革咨询为大家进行精益生产管理七大浪费详解:
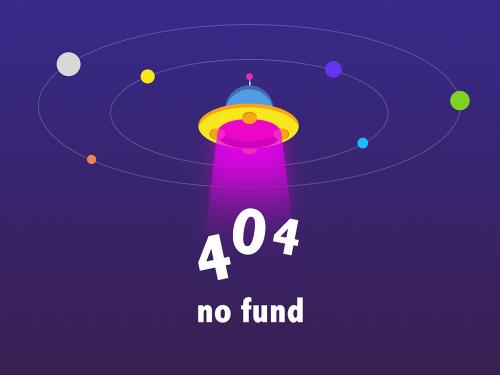
超过生产计划或提前完成一点也不值得骄傲。这只是在浪费的时候、生产了浪费的数量的浪费物品、制造了过盈生产的浪费。现如今,所有企业为了实现将「需要的物品,在需要的时候, 供给需要的数量」这种所谓的jit(just-in-time)而展开着改善活动。但是,对「需要的物品,在需要的时候,供给需要的数量」这句话的理解是多样的。jit生产方式所达到的状态是指在接到顾客订货的同时就开始生产,并使其在指定的时间到达到客户手中的状态即,发出仓库中存在的成品库存没有任何意义。汽车的情况是,从确定汽车制造商的最终组装线计划时点开始生产,但是从调配材料或部品进行生产,然后将产品运送到各销售点和代理店,并完成各种手续到达顾客手中需要最小限度的时间。
「过量生产的浪费」是指进行顾客订货以外的生产。 尤其是无视日程计划的过盈生产更是荒谬。还要完全否定「 都能卖出去」的思想。为此,是以改善的观点上所说的「以要求的tact进行生产」为大前提。营业和生产管理部门只按照交易单位的信息来生产是不行的
另外,制造部门若是认为以自己会社生产管理部门的日程计划进行生产就一点问题没有也是不行的。不要忘记信息和日程计划都是以预测为基础的,是包含「过盈生产」风险的。
特别是各经销商店是以10台、20台这样的少数量来要货。很多情况下生产管理部门是将这些少量订货以50和100的生产单位合并在一起下指示,发货时从中进行发送。于是,剩余的数量抱着「会在什么时候发出去的」的安逸心态放置,结果在几年后的年末结算上却成为处理损失而进行了财务处理。
另外, 「过量生产」还有一个问题点。企业不管采用什么方法,所确立的都是以月为单位进行生产的体制。虽然是以生产计划为基础来研究制定加班计划、设备运转计划、材料部品的调拨计划等,但每个方面自不能有多余部分以免形成投入的余量。于是在实际生产中,若过多制造某特定部品,就不能制造其他的部品。现在重要的不是要实现合计数量而是要严守各部品别的计划。通常, 都是不责怪多生产部品的行为而是只追究少生产部品的行为, 这样的管理不能称为管理。
2、库存的浪费
多余的部分作为过盈生产所产生的浪费,在丰田生产方式中将其称为最不好的浪费。这部分是因机器的增设、材料的事前入库、多余的作业者、利息的增加、仓库的增大等而导致的,是有百害而无一利的部分。库存与产品产生附加价值没有任何关系。库存只会掩藏生产和流通中所发生的问题点,因此,要减少库存,越少越好。
因库存而产生的问题点数也数不完。因库存而产生确保保管库存的仓库和容器、出入库的搬运器具和人员、管理库存的各种机器帐表以及人员的有关费用,以及在成为长期积压库存情况下的质量保证费用和处理损失费用等。一般需要15 ~ 20%左右产品单价的维持费。特别是高价产品和体积大的产品会达到30 ~ 35%。另外,因存在库存,众多的问题点不能显露出来(可视化),而且企业的生产体质绝对强化不起来。因此,将库存当做「罪过」而努力削减。库存只是管理·监督者为了高枕无忧而准备的安心剂。
3、搬运的浪费
jit 生产是从搬运开始的这种说法一点也不过分。要认识到从手「伸出」「移动」「拿来」「放下」开始, 台车(pallet)的移动,「由仓库到工厂」「由工厂到机器」在「作业者的手所涉及的范围」移动等,这些全部都是不合理。只是单纯地从工厂内的一个地方移动到另一个地方这种物流,其间绝对不会产生附加价值。不是要改善搬运作业的行为本身,而是要消除它,消除得越多,竞争力就越会增加。
最小限度的搬运是指「one work·one touch」。搬运虽然是生产中必不可少的作业,但要将其减到最小限度是关键(point)。改善「搬运」可以考虑进行自动化和使用无人搬运车,但首先要考虑废弃搬运本身。从工程的布局来看,可以说「全程连续的line化」是理想布局。若只将一部分工程设置在工程之外, 或虽是同一工程却将要进行全程连续作业的工程设置在不同的建筑物内就会发生浪费的搬运。由于存在不这样做就不行的理由和企业的方针,因而不能一律地判断是好是坏,但,这是浪费一点错没有。为了进行全程连续流水线化, 需要解决技术和工艺方法的开发、设备可靠性和灵活性的改善, 以及采购政策的研究等多项课题。而且,对line内各工程间的间隔,为了「修理」要达到能拽出产品的最小限度。虽然根据设备的大小要有所不同, 但设备长度在2 ~ 3m的情况工程间最大间隔限在10 ~ 20cm 左右就可以。为此,需要将设备的各种阀门、开关、仪表、机油容器等从侧面移到前面或后面, 设备设计面上的研究是最关键的要点。并且工程内放置部品的场所?谝宰匀坏淖耸粕焓志湍茏プ〔返姆段?而不需要向前弯身或踮脚,或转身,即,正常是在60 ~ 70cm 以内。以购入品的包装单位大为理由而临时放在线体的旁边少量地分批拿出来使用,由于这也是移动,因而需要改善。
4、等待的浪费
机器自动加工时只是在旁边站着监视的作业方法即使作业者想要做什么,可由于机器在运转而没办法作业从而产生了浪费。是因等待作业的富余时间而产生的浪费。但是由于这种浪费易于发现而且不会诱发别的浪费,所以比别的浪费容易改善。由于现场管理者是考虑了单位的环境和作业因素来直接创建现场的人,因而对现场有自豪感,所以看不出等待的浪费。而且根据自己的想法发表着「这个作业就是这样。多少会有些等待, 但由于做了最大限度的改善,而难以进一步改善」这样的见解。 这些人中有很多人认为「由于人不是机器人, 所以不能1秒、2秒一点不差地满负荷作业。是需要有少量余量的」。是存在象组装作业一样没有等待作业的地方的。在「同样的劳动, 同样的报酬」的观点上,消除等待也可以说是现场管理者的重要任务.
5、动作的浪费
指的是在产品的制造过程中没有附加价值的人的行动或设备、机器的动作。找部品或制造不良品等…。作业场所中能发生浪费的原因要多少有多少而且无时不在。工厂里的所有事物都在动,人们步行、说话、打电话、开会,机器也在运转, 水也通过管道流动,全部都是动态的活动。但是不是所有的动作都给产品带来附加价值,不能给产品带来附加价值的活动就是浪费。动作的浪费是十分细小行动的浪费。因此动作的浪费具有很不易被发现的性格。例如, 为了拿住部品而进行方向转换, 固定夹具时多次调整的动作,或者是安装时按压的动作等等,有很多象这样非常细微的动作。将持续按压部品和开关的动作称做按摩,按摩不要在公司做,还是回家给老婆做比较好,
工厂没有理由在按摩上花钱。动作的浪费由于极其细小,所以要仔细观察 「一举手一投足」,并通过动作分析进行改善。要修整夹具和产品的形状、精密度, 以彻底遵守标准作业。
6、加工的浪费
产品是要对原材料进行某种形态的加工才能做出来,有多种加工的方法,这若干种方法中的哪种方法能比别的方法更有效, 而哪种方法又不如别的方法呢,要进行不断的改善。“从很早以前到现在一直都是这样做的,而且别人也都在这样做”等这样的思考方式是不能提高竞争力的。「加工的浪费」是最能显示技术力的地方。在电弧焊中,您想使机器手产生火花的百分比达到多少呢?若是60%, 那么,若不具备部品固定方法以及与他工程的编成方法、部品的设置方法和线路管理或部品的精密度等多种条件,也是达不到该数值的。而且,即使是产生火花和切削碎屑的作业, 有过多消除毛刺和磨边作业的加工也是问题。这不是以自己会社的水准来判断的,而是要掌握竞争会社的信息和加工业种的水平,以与高水平进行比较来判断的。 若只是以自己会社的水准来判断而在竞争中败下阵来,那就什么也不是了。
7、不良的浪费
不良的发生确实是挡不住程度的巨大浪费。制造不良品由于是制造了卖不出去的产品, 也就是制造了浪费的产品。虽说如今已经没有必要再对「不良」其本身进行讨论, 可现实又如何呢?向消费者提供良品是进行企业活动的大前提。为了这些消费者,不是要依靠最终工程的检查或挑选来保证的, 而是要在各工程内达到绝对不产生不良品来进行制造的。可是, 虽然制定了这样的方针, 但现实上却不能说是彻底达到了。在「彻底保证自己工程的品质」的帷幕下有很多装有不良品的不良品箱。倘若这些不良品箱以1个月或1周的量堆放,则证明改善没有得到实行。特别是,有时会发现在铸造、压铸、树脂等中存在 「若能熔化就再使用」或在机器加工中存在「尺寸再大一点还行」等recycle(循环利用)的想法。这是荒谬的错误。说出这中话的现场管理者是没有资格的。以某企业为例,若产生了一个不良, 部品的价格上就产生3倍的费用。不良不仅在费用层面上负担相当大,更重要的是反映了企业在对待顾客的姿态上有问题。若要消除不良的浪费,关键是通过遵守规定的技术加工条件,进行彻底的标准作业来保证质量,而且,重要的是还要针对细小的问题,向设备·夹具和产品设计的流程流逆流而上来推进改善活动。
作者:博革咨询
咨询采购表
精益生产怎么做?六西格玛咨询怎么做?项目周期是多少?大概需要多少费用?
我是什么企业?目前需要解决的问题是什么?预算周期是多少?想要达到什么效果?
欢迎您浏览博革咨询官方网站!我们专注于精益生产咨询、六西格玛咨询、精益供应链咨询、5s6s现场管理、tpm设备管理咨询、工厂布局规划、目视化看板设计等领域的落地咨询;若对本页面内容不感兴趣或想了解更多与您企业、行业相关的资讯,可通过以下方式寻找解决方法:
(1)工作时间可拨打我们的全国咨询热线:15721533189,021-62373515 进行咨询;
(2)在网站栏目右侧“搜索框” 输入您感兴趣的关键词,搜索相关内容;
(3)点击左侧“在线咨询”按钮, 您可以和我们的专家老师在线咨询;
(4)非工作时间请点击网站下方的“留言” 按钮,留下您的z6尊龙旗舰厅的联系方式和需要咨询的内容,我们将安排专业顾问给您解答;
(5)入群方式:扫描左图二维码,添加小博微信好友,通过认证后,加入精益生产vip会员微信群。
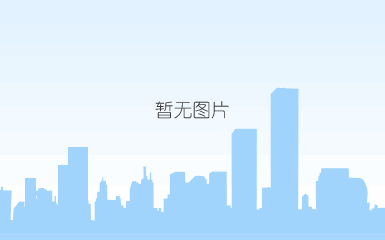
热销课程 hot
相关内容 related
- 6s现场管理法—清洁实施的方法步骤10-25
- 6s现场管理法—整顿实施的方法步骤10-22
- 6s现场管理法—整理实施的方法步骤10-20
- 5s管理推进的6定原则10-18
- 什么是定置管理?09-28
- 5s管理活动的推进条件09-19